Abstract
This article provides a comprehensive examination of color protection films (PPF), especially focused on modern pure film protection technology. We dive into scientific principles that support their protective abilities against physical impacts, ultraviolet degradation and chemical contaminants. The discussion emphasizes how these advanced polymer layers serve as a key barrier, maintain car aesthetics and value, while considering key factors for optimal performance and innovation of material.
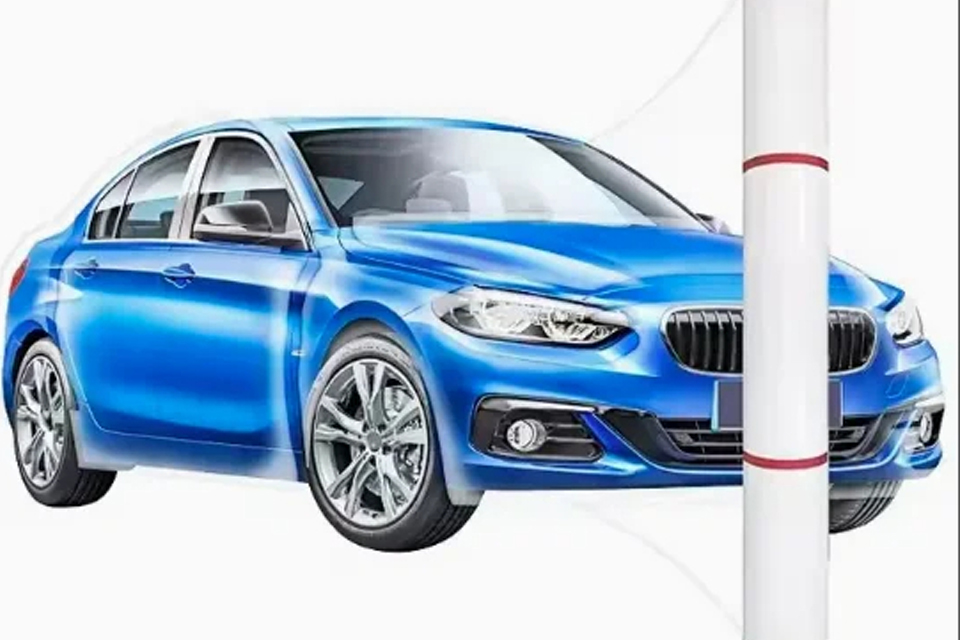
Protective power of color protection films: scientific overview
The question of whether the PPF (PPF) film actually provides its promise of the automotive industry is common among the enthusiasts and vehicle owners. The positive answer is rooted in material science and engineering: PPF, especially high -quality color protection film, works as a robust sacrificial barrier. This transparent layer is designed to absorb and distract harmful forces and environmental aggressors, maintaining the original painting work of the vehicle, maintaining its visual attraction and potentially averting costly restorative procedures.
1. Protection mechanisms: How PPF protects your vehicle
Color protection films offer multilateral defense for automotive surfaces.
The attenuation of the impact of the main function of PPF is to ensure resistance to physical impacts. These films, which are usually composed of elastomeric polyurethane, are designed to absorb kinetic energy from projectiles such as stone chips, gravel and road fragments. This energy absorption prevents the impact of achieving and breaking the clear coat of the vehicle and the underlying layers of the color, thereby averting chips and pitting.
The ultraviolet (UV) radiation shielding extended exposure to sunlight is the primary cause of color fading (photodegradation) and oxidation, leading to a boring and aging appearance. Advanced color protection films include UV inhibitors into their structure. These inhibitors block a significant percentage of harmful UV rays, effectively slow down the process of degradation of the underlying color and maintain its liveliness and shine.
Resistance to chemical contaminants non -porous, chemically inert quality PPF quality offers excellent resistance to a range of environmental and chemical contaminants. This includes acid birds’ droppings, corrosive insects, spray trees, trees, road breath and mineral deposits of hard water. By preventing these substances from etching or gluing, PPF helps maintain an untouched finish.
Minimization of surface scraps of everyday wear, such as light scratches from washing cars, disgraceable zippers or brushing against the vehicle, can hit the surface of the color. PPF provides a durable layer that resists these small classes. I protect against such imperfections significantly reduce the need for frequent color, touches or larger corrections, which maintains the integrity of the factory surface.
The skills of self -healing remarkable technological progress in Premium Protection Films is the integration of the “self -healing” top coat. This layer, often specialized thermoplastic polyurethane, has viscoelastic properties. When exposed to small scratches or swirls, the use of slight heat (eg from sunlight, warm water or thermal pistol) allows the film the film to reflect and repair these imperfections and restore its smooth, high glossy appearance.
2. The Technology Behind PPF: Materials and Innovations
The efficiency of color protection films largely depends on their composition of the material and the technology built into them. Early films were often made of PVC (polyvinyl chloride), which were limited in terms of flexibility, clarity and longevity.
Modern, high -performance PPFs are mainly made of thermoplastic polyurethane (TPU). TPU offers higher elasticity, optical purity, stain resistance and durability compared to older materials. In addition, TPU is the basis of the above self -healing properties. These movies are usually designed in multiple layers:
Adhesive layer: adhesive sensitive to pressure designed for a strong connection with the color of the vehicle without causing damage after removal. Polyurethane base layer: core protective layer providing impact resistance and flexibility. Topcoat: Often a clear, polymer layer, which provides chemical resistance, UV protection and in advanced films, self -healing properties.
This advanced construction ensures that clear paint protection film remains virtually invisible while offering maximum protection.
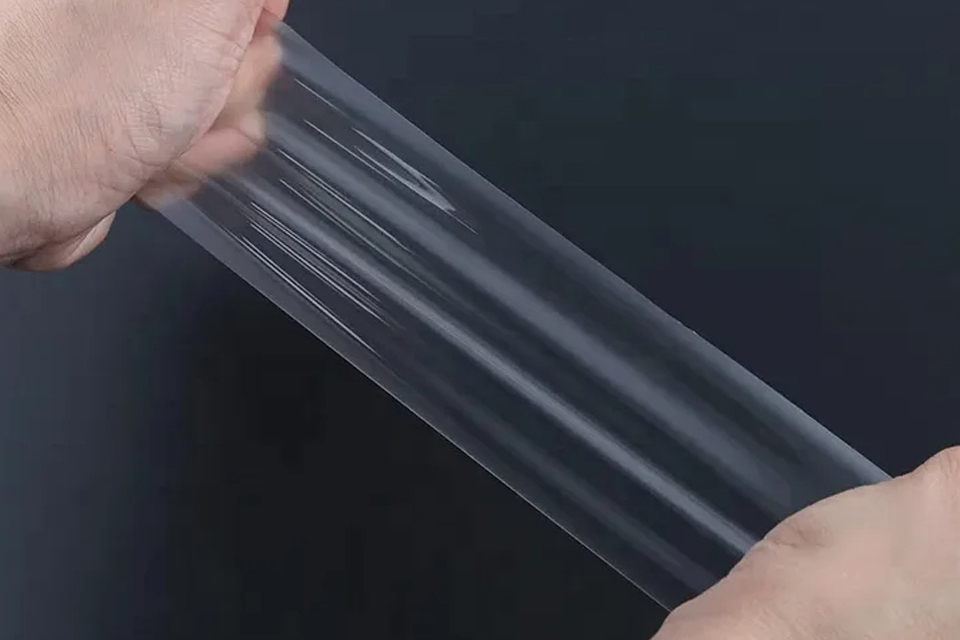
3. Comparative Features of PPF Technologies
Feature | Standard TPU PPF | Premium Self-Healing TPU PPF | Older PVC PPF (Less Common Now) |
---|---|---|---|
Primary Material | Thermoplastic Polyurethane | Thermoplastic Polyurethane | Polyvinyl Chloride |
Impact Resistance | Good to Excellent | Excellent | Moderate |
UV Protection | Good | Excellent, non-yellowing | Fair, prone to yellowing |
Self-Healing | No / Limited | Yes (for minor scratches) | No |
Clarity | High | Very High, optically clear | Moderate, can degrade |
Stain Resistance | Good | Excellent | Fair |
Durability | 5-7 years | 7-10+ years | 2-4 years |
Flexibility | High | High | Lower |
4. Critical Considerations for Optimal PPF Performance
To maximize the benefits of paint protection film, several factors warrant careful consideration:
- Film Quality and Manufacturer The market offers a range of PPF products. Opting for films from reputable manufacturers known for their research, development, and stringent quality control is crucial. These films generally offer better clarity, durability, and protective features.
- Professional Installation The skill and experience of the installer are paramount. Proper installation involves meticulous surface preparation, precise film cutting (often computer-aided), and expert application techniques to ensure an edgeless, bubble-free finish. A poor installation can compromise both the film’s appearance and its protective efficacy.
- Strategic Application Areas While full vehicle wraps are available, PPF is most commonly and cost-effectively applied to high-impact zones. These include the front bumper, hood (full or partial), front fenders, side mirrors, rocker panels, door edges, door handles, and the rear bumper luggage.
- Projected Lifespan and Warranty The expected lifetime and guarantees of quality color protection films usually come up with the manufacturer’s warranty ranging from 5 to 10 years or even longer for premium lines. This warranty usually includes defects, such as yellowing, bubbling or cracking, providing peace of investment.
- Appropriate Maintenance and Care While PPF is durable, it is not indestructible. Regular washing using pH-neutral car wash solutions and safe washing methods (e.g., two-bucket method) is essential. Avoiding harsh chemicals or abrasive cleaning tools will prolong the film’s life and appearance. Some manufacturers offer specialized PPF care products.
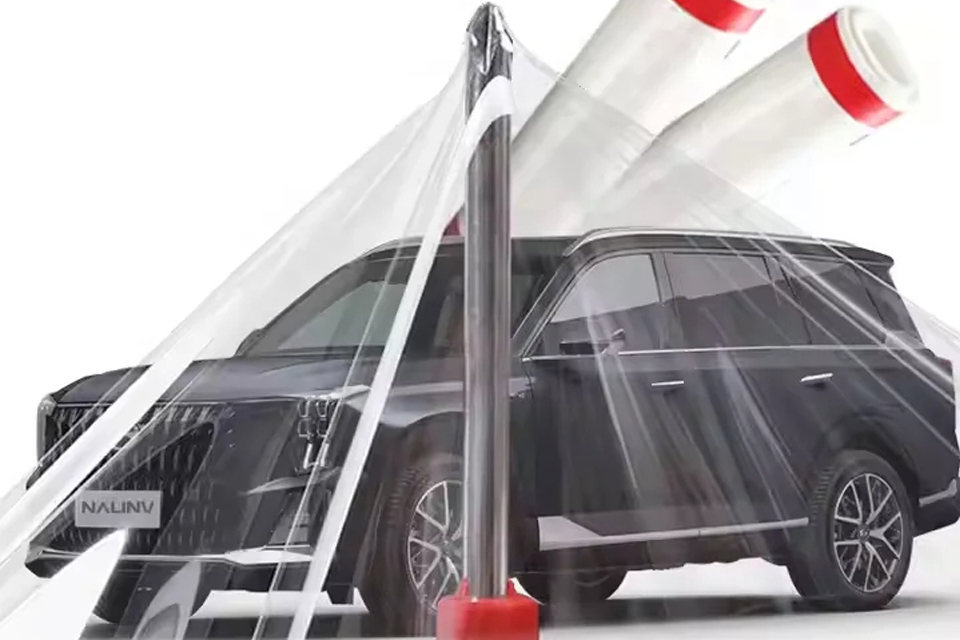
Conclusion
In short, modern color protection films, especially pure color preparations for advanced TPU technology, offer scientifically proven and highly effective means of maintaining automotive painting. Their ability to absorb impacts, resist chemical etching, block UV radiation and even smaller abrasions from their cleaning makes them an invaluable benefit for vehicle owners trying to maintain the untouched condition of their car and the value of further sales. The key to unlocking their full potential is to select a high quality film, ensure professional installation and adherence to recommended maintenance procedures. As a result, PPF stands as a sound technological investment for long -term car surface protection.